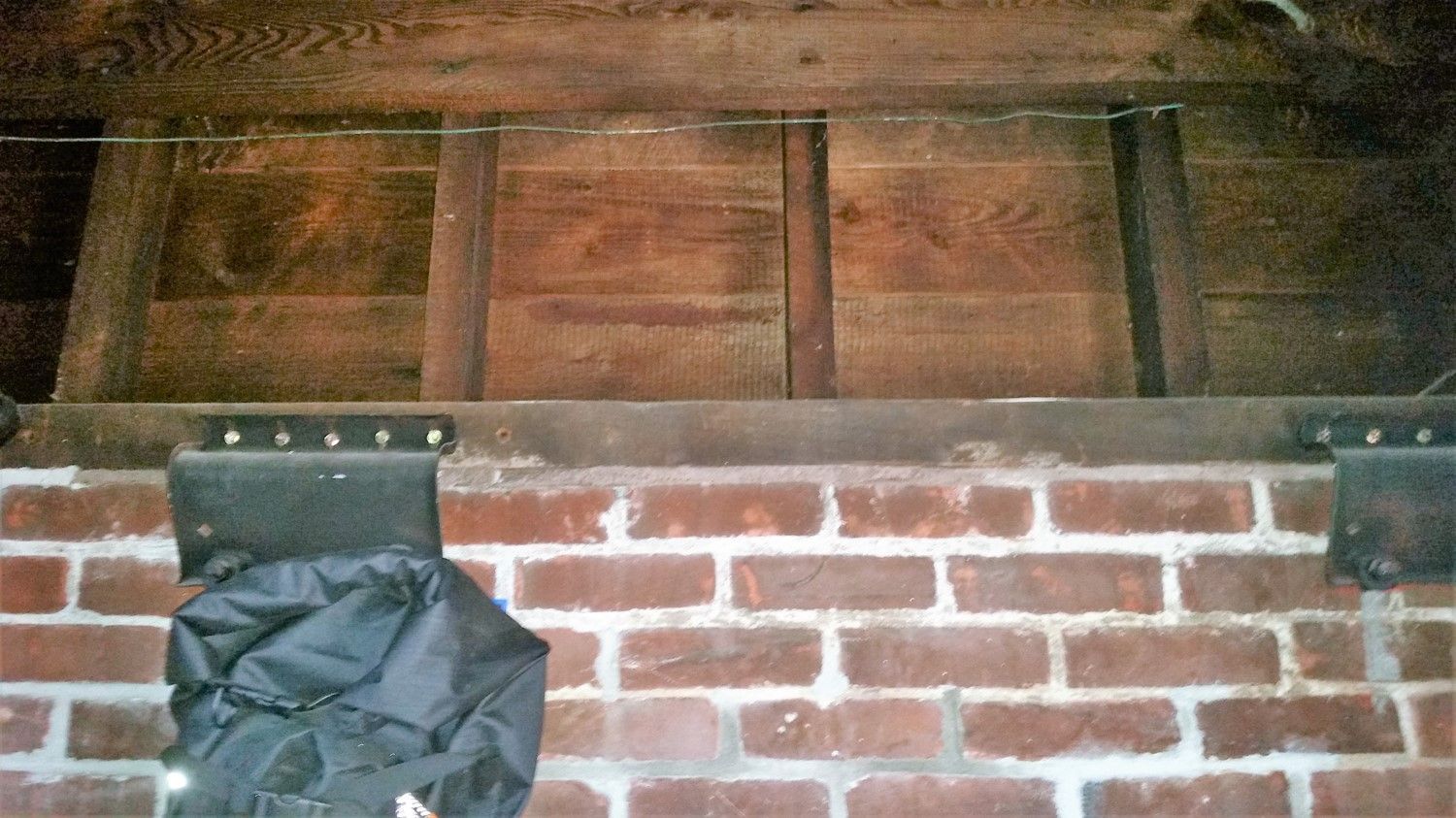
Buyer beware, Pt. 1
A handyman’s work cleared the low bar for an earthquake insurance policy. See how we addressed the issues found here and how the homeowners can rely on tour retrofit to work, instead of relying only on earthquake insurance.
Buyer Beware, Pt. 2
Michael covers incorrect hardware usage, improper installations of the correct hardware, and techniques to address special circumstances. This work was performed by another seismic specific retrofit contractor, not just a handyman.
Buyer Beware, Pt. 3
While attempting to perform a seismic retrofit, this foundation repair contractor (not a seismic retrofit contractor) came across insulation that seemed to prevent a necessary connection from being made. Instead of maneuvering around this minor complication with simple engineering, the company left the project partially finished. This retrofit was ineffective without all connections made.
Buyer Beware, Pt. 4
This retrofit was installed by a waterproofing company hired to waterproof a crawlspace. Michael discusses how these homeowners paid too much money for a retrofit which after an earthquake, may disqualify homeowners from compensation from their insurance company.
Buyer Beware, Pt. 5
Another example of hardware installed by a general contractor that doesn’t quite qualify as an effective retrofit. Michael describes the math that goes into designing a retrofit and how NW Seismic will supplement the existing hardware.
"Retrofits" Gone Wrong
Don’t pay for your retrofit twice. Click on the images below to learn why these photos are concerning for both homeowners and seismic contractors.
-
Non-Bolted UFP 10
ButtonAlthough this UFP 10 is the correct hardware, its value is negated by its improper installation. The contractor who installed this particular side plate ignored the poor integrity of the foundation. As the side plate was installed, the foundation crumbled away. You can clearly see there is no screw anchor on the left, because the foundation isn't there to hold it in place. The other screw anchor won't be effective as it isn't secured within the surrounding foundation.
-
"Retrofit" on a Brick Foundation
ButtonBrick is a material that will not withstand seismic activity, so anchoring to it is useless. If in another world anchoring to brick was an option, many crucial connections were still missed. The cripple was was not addressed and clips were not installed at the top plate.
-
Wrong Hardware
ButtonA handyman provided this completely untested method of "retrofit" for a homeowner. We were told he said he, "thought it would work".
-
Ineffective Nail
ButtonThis nail was driven so far into the lumber that it cracked the veneer. The veneer is an important element for the lumber's structural integrity. Once compromised, the lumber loses shear resistance.
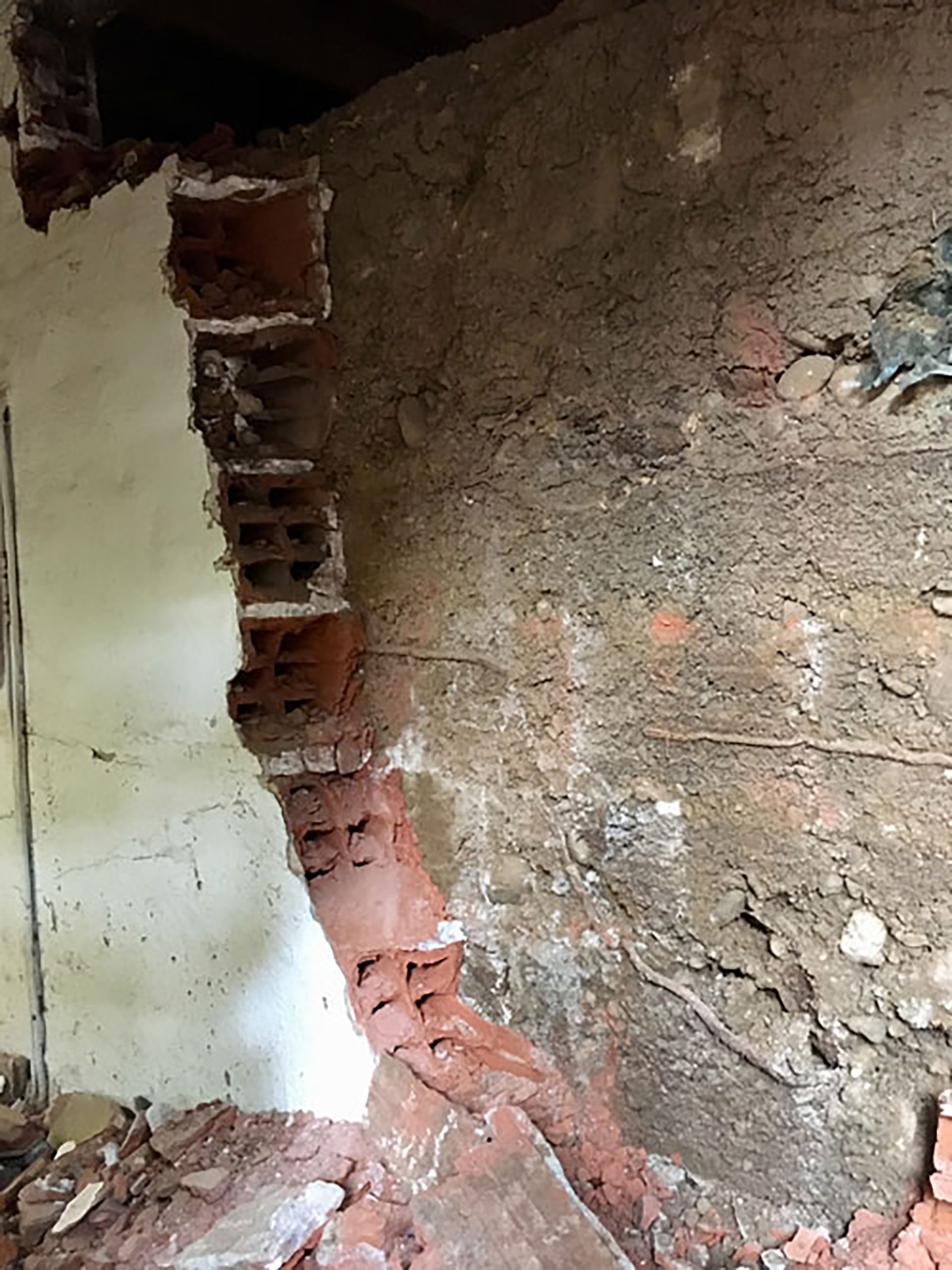
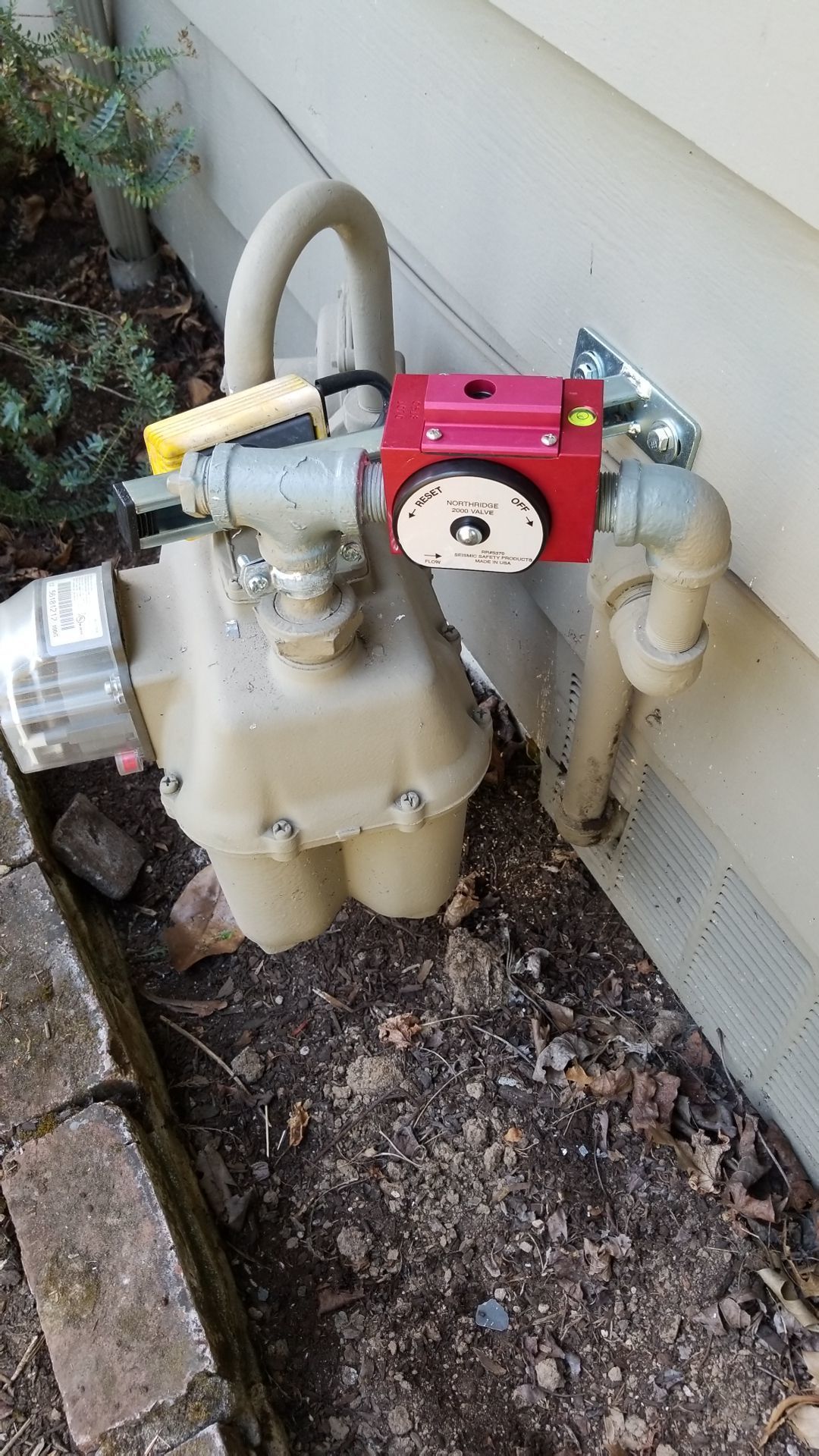